The other half-finished big-ticket project that came with the house (besides the chimney) was central air conditioning. The house had been fitted with supplies and a return for high-velocity air conditioning, and lines had been run for a condenser and air handler, but no units had been installed.
High-velocity AC is a special system, manufactured almost exclusively by the Spacepak brand, that uses flexible supply lines that are much smaller than the ducts in your typical central air system. It’s useful in old houses because it can be run through narrow existing spaces rather than a costly renovation or adding exposed ducts. While this made it a sensible choice for our house, the downside was that it’s a somewhat specialized system that not every HVAC contractor deals in. And yes, it’s very inconvenient that “high-velocity air conditioning” abbreviates to HVAC but that is already taken by the industry category of “heating, ventilation, & air conditioning”.
Central air conditioning is a big perk here in the land of humid summers, but a half-finished system wasn’t worth much unless it could become fully finished. During the inspection phase of the sale, I called around to gather estimates on roughly how much it would cost to finish the installation. This was a difficult task given that we didn’t own the house yet and I had limited information about how much needed to be done, and unsurprisingly I received a number of unhelpful answers from HVAC contractors. However, Jason from Stafford Home Service not only called me back, but took the time to ask some questions about the project and ballparked it at $5,000. I appreciated this, and it earned them some business down the road, since when it came time to tackle the project, they were the first ones I called for a quote.
I got several other quotes in addition to Stafford’s. One guy delivered a rambling monologue that apparently ended with a recommendation that we abandon the high velocity system and install some combination of ductwork and mini-splits. I feel like that guy could have saved both of us some time by just saying “I don’t work with high velocity systems” the first time I contacted him. Pronto sent a salesman to do the quote and came back with an absurdly high price, something in the range of $15,000. That one felt very much like they pulled a number straight from their Price Book for Suckers and didn’t even bother factoring in the cost savings from the existing work. Did I mention I hate gathering quotes? I hate gathering quotes.
Stafford initially came back much higher than I had been expecting as well, but after some back and forth they came down substantially, to $7800. This was more than I had been hoping to hear, but was still within the range that I had expected it might be. One thing driving the higher price tag was that most of the contractors I spoke with urged me to install a more powerful system than the previous owners had seemingly planned for, which also mean installing more supply lines to distribute the additional air. I suspect we could have gotten by with a less powerful unit, since the house is well insulated and we don’t cool it to 62℉ like a bunch of maniacs. But, I wasn’t going to totally disregard professional advice, and it would be a shame to spend all this money installing a system only to have it underpowered and struggling to keep up with a Minnesota summer.
Installation
After another planning visit and some more discussion, we came up with a plan to distribute the additional supplies: several more in the kitchen, one more in the largest bedroom on the second floor, and the rest in the attic, which was soon to be a finished space and would certainly be one of the warmer parts of the house.
Installation happened over the course of about three days. The first day involved a big crew of about five people, while the next two days were calmer with 2-3 people. Jeremy was the leader of the crew and was a delight to work with (I’ve seen him about once a year since, for other projects and followups). The crew did a great job of not making a mess and was good about consulting me before making important decisions.
They wrapped up on July 20th, and then we proceeded to have an abnormally cool and cloudy summer and never needed to actually use air conditioning. What a grand christening! We did make good on our investment starting in the summer of 2018, which brought a number of prolonged heat waves. The system works very well, runs quiet, and has no trouble cooling the house.
A few small imperfections: There are a couple large flexible ducts supplying some of the lines that I don’t love. These might have been avoided if all the supplies had been placed during the initial installation, when some of the areas to run lines were more accessible. One of the big ducts runs across the ceiling of the laundry/utility room in the basement, which is not a huge deal because it’s the laundry/utility room, but it does encroach on the headspace a bit.
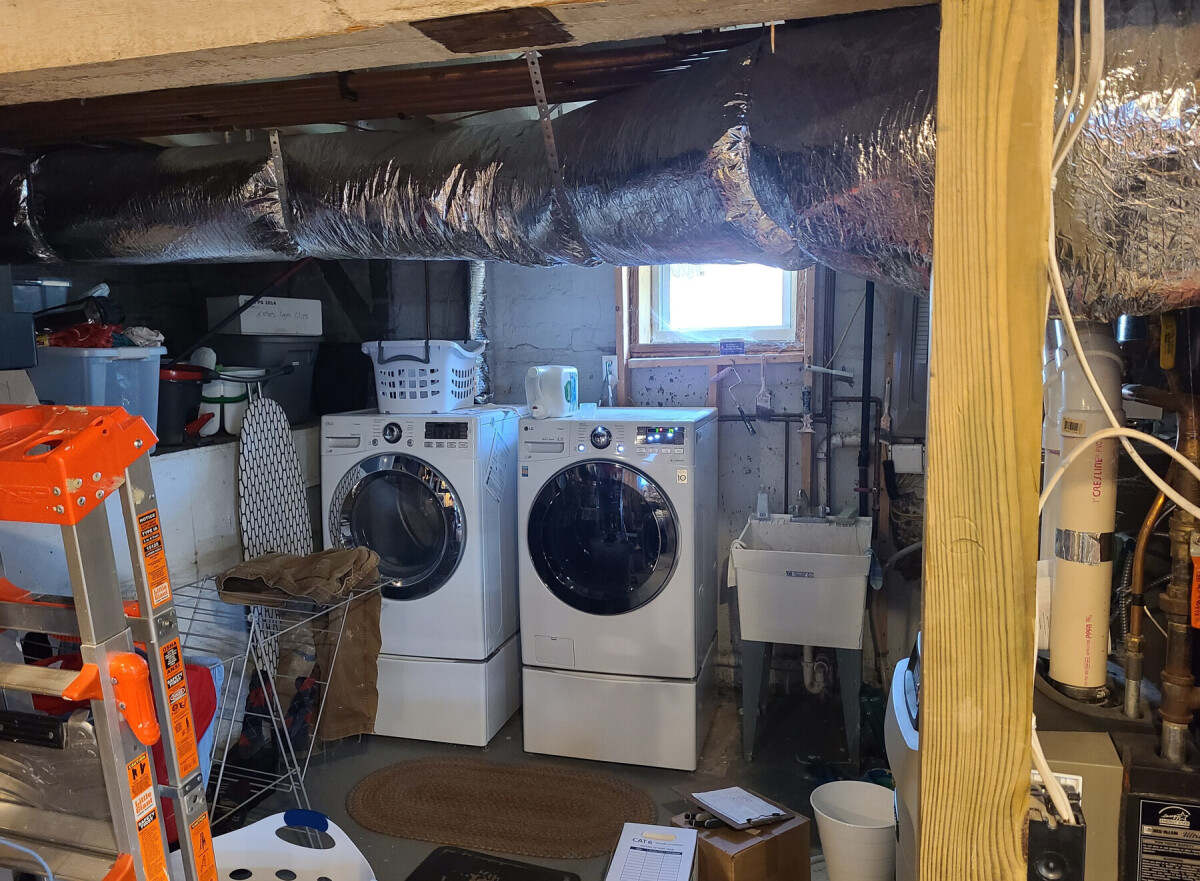
The other runs around the edge of the attic. This could have been a real nuisance, but it worked out okay. We were already planning to build kneewalls on the slanted sides and could enclose it in those. The part passing under the window will eventually be turned into shelves and a window seat, which is a good use for that space. Still, it would have made life a little easier not to have to work these ducts into our plans.
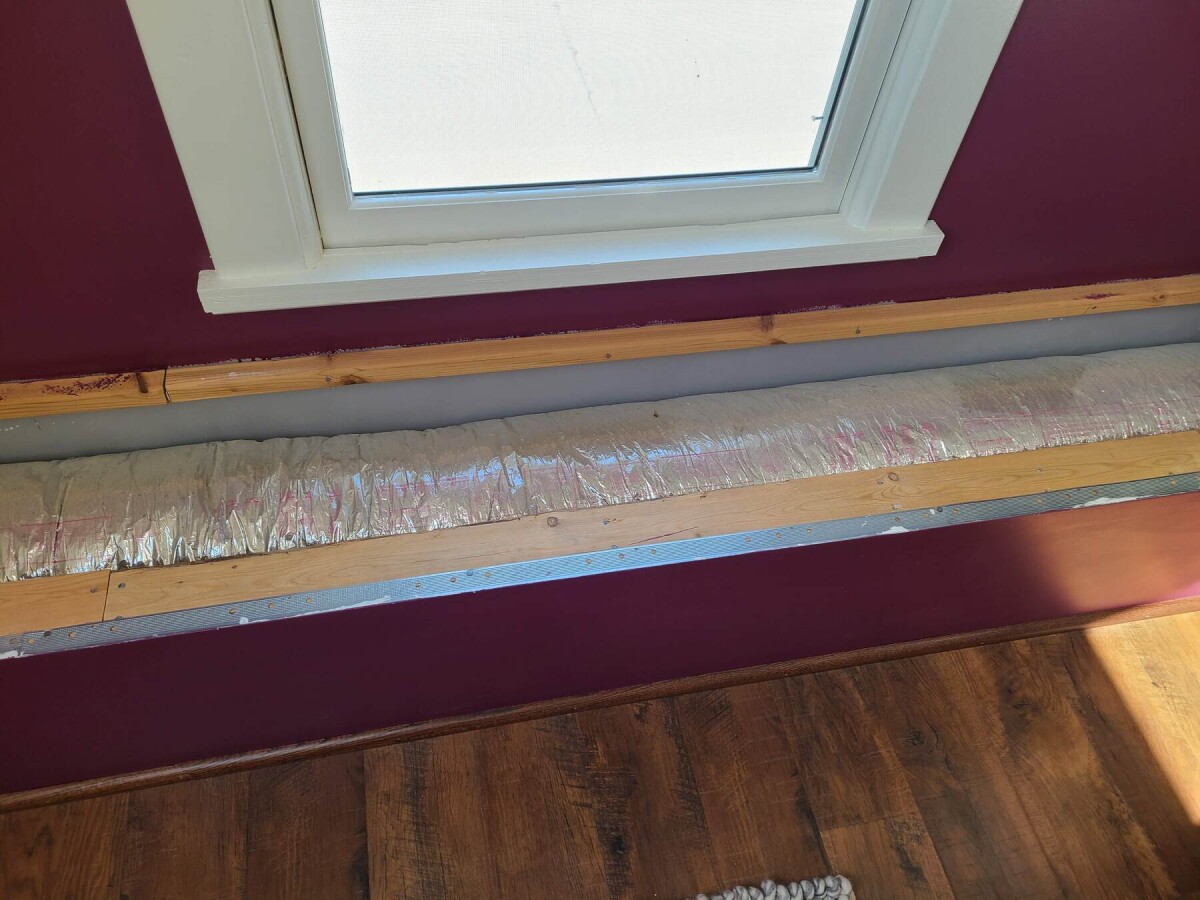
Part of the housing for the attic duct, to eventually be capped.
The only real complaint I had with the crew’s work was one spot I didn’t notice until after the job was done where they had routed a line in front of the attic’s small porthole window in a way it couldn’t be enclosed without blocking the window. Frustratingly, the crew did a great job of communication in general and consulted me on a whole bunch of decisions where I was fine with what they wanted to do. This was the one time that I wouldn’t have liked their plan, and of course it was the one thing they didn’t check with me on. It was a good lesson to me that yes, I should check in frequently on work that’s happening and not feel too guilty about bothering the workers. Luckily, this problem was pretty easily fixed. By dropping the supply on the right side of the opening instead of the left, we could avoid the need to cross that part of the room entirely, and it still came out in a good part of the ceiling in the floor below. I had our attic contractor relocate it when they were building the kneewalls, and it’s fine now.
Dog Tax
My goal with this blog is to give you all the info, even when it’s a little dull. Not every bit of owning a house is glamorous Instagram reveals, and I think it’s worth talking about the frumpy parts too. However, I feel bad about subjecting you, my audience, to extensive posts on topics that do not inspire or excite.
So I’d like to propose a deal. Whenever I write a post I deem sufficiently boring, I’ll reward you at the end with a cute dog photo, starring Rigby, our weird ornery lab/pit mix that we adopted in the same year as the house. Hopefully this will be a worthy token of my appreciation for sticking it out through the less interesting moments of home improvement. And look, if you didn’t actually read the whole thing and just scrolled straight down here to find it? Well, that will be our little secret.
Here’s your first installment of dog tax:
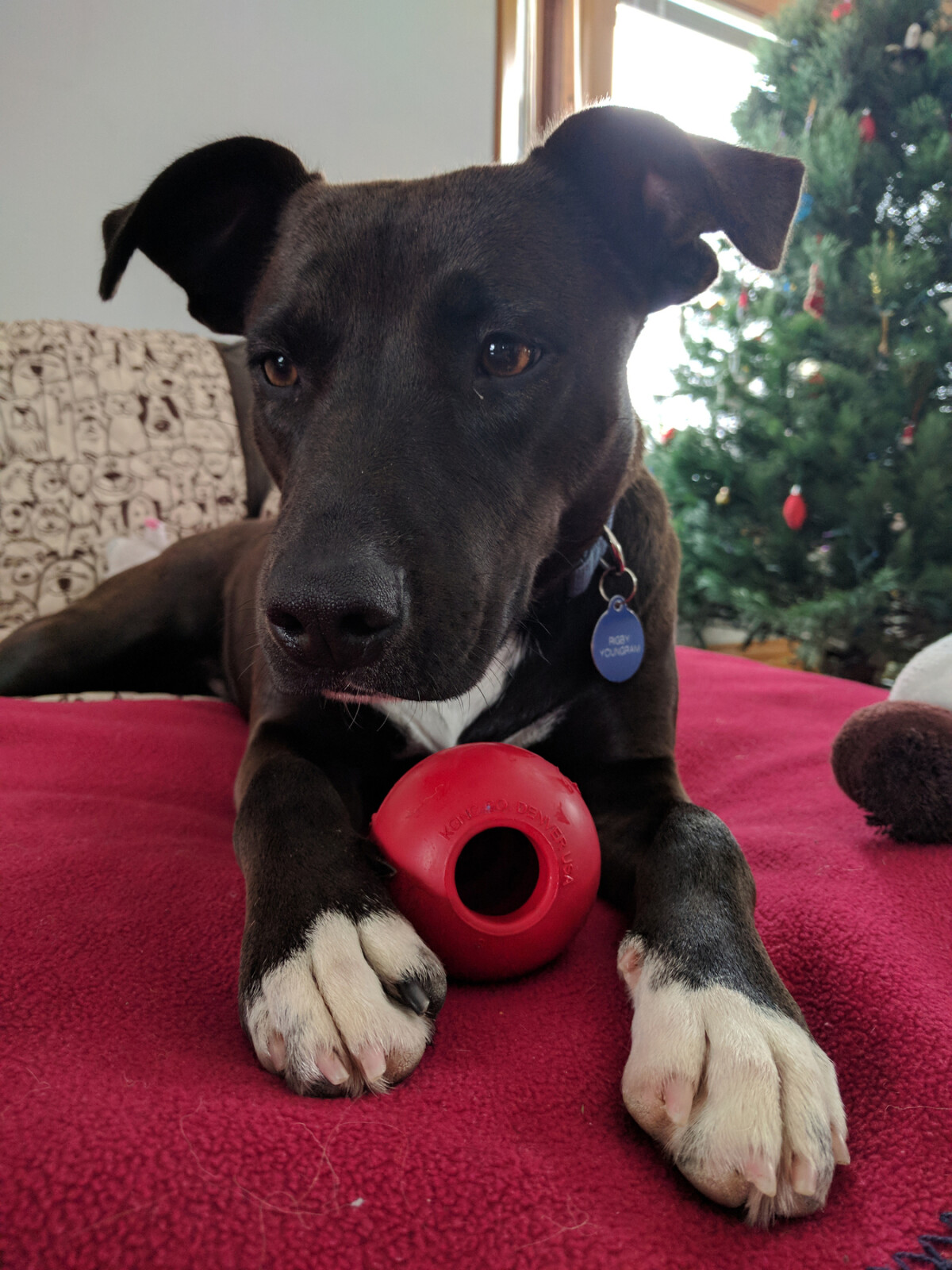
Time & Materials
All labor and materials | ||
---|---|---|
Daikin DX16SA030 outdoor condenser | ||
6 new supply lines | ||
Electrical wiring | ||
Labor | ||
Permits | ||
$7,800 | ||
Sale of old window units | -$120 | |
Total | $7,680 |